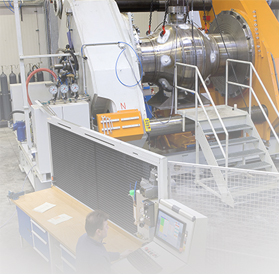
Maintenance Manual of high voltage flame arrester
date:2021-07-01 13:43
1) In order to ensure the performance of high pressure flame arrester reaches the purpose of use, before installing the flame arrester, the manual provided by the manufacturer must be carefully read and the label shall be checked to see whether the requirements of the pipeline are consistent.
2) The flow direction mark on the flame arrester must be consistent with the flow direction of medium.
3) Check every half a year. Check the fire barrier for blockage, deformation or corrosion.
4) The blocked fire resistant layer shall be cleaned to ensure that each hole is smooth. For deformed or corroded fire resistant layer, it shall be replaced.
5) When cleaning the core parts of flame arrester, high pressure steam, non corrosive solvent or compressed air shall be used for purging, and sharp Hardware shall not be used for cleaning.
6) When re installing the fire barrier, the gasket shall be updated and the sealing surface shall be confirmed to be clean and free from damage and no air leakage shall be allowed.
General selection principle
The safety fire resistance speed of the selected flame arrester shall be greater than the flame propagation speed that may be achieved at the installation position.
When there is no other anti tempering facilities, flame arresters shall be set for the combustible gas transmission pipeline connected with the burner.
Flame that prevents the propagation of subsonic velocity should be stopped by using flameproof flame arrester, and its installation position should be close to the fire source;
Flame that prevents the propagation of sound or supersonic shall be flame arrester with detonation resistance, and its installation position shall be away from the source of fire.
For the different nominal diameter of detonation arrestors, the required distance from the ignition source * small installation distance is shown in the table.
For flame arresters used in cold areas, some or integral shells with heating sleeves shall be selected, or other heat tracing methods can be adopted.
In special cases, flame arrestors with flushing pipe, pressure gauge, thermometer, drain port and other interfaces can be selected as required.
When the nominal diameter is less than DN50, the flame arrester installed at the pipe end should be connected with thread; When the nominal diameter is greater than or equal to DN50, flange connection shall be adopted.
Flame arrestors installed in the pipeline shall be flanged.
The flame arrester installed at the pipe end shall be equipped with rain proof ventilation cover which can be opened automatically.
The flame arrester on each branch pipe of gas connected pipeline between tanks shall be of detonation resistant type.
For the oil and gas discharge pipeline at the top of the tank, the detonation proof flame arrester shall be selected at the connection with the tank top.
The detonation arrestor shall be selected on the header of protective gas and oil and gas discharge pipeline at the top of the tank. Emergency vent pipe shall be set
Flameproof flame arrestor.
Detonation arrestors shall be provided between the main oil and gas discharge (or recovery) main pipe of the loading and unloading facilities and the gas phase pipelines of each branch pipeline.
Before the combustible gas vent pipe is connected to the torch, if the flame arrester is set, the detonation proof flame arrester shall be selected.