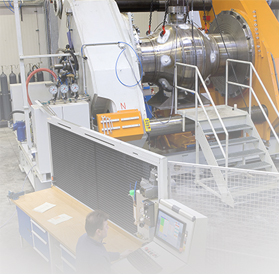
What is the difference between the upper and lower discharge valves
date:2023-07-12 10:42
The difference between the upper and lower discharge valves is that the flange is different. The general diameter of the upper discharge valve is different, while the lower discharge valve is generally variable in diameter. The flange at the end of the reactor is installed one level larger. The opening and closing directions of the valve disc are different. As the name suggests, open the valve disc and lift it up to the reactor. As the name suggests, open the valve disc and lower it into the valve chamber. For this reason, it is necessary to increase the flange level and increase the valve chamber space. The copper nut is different from the copper nut of the upward expansion discharge gate valve, and the copper nut of the downward expansion discharge valve stop valve. The opening and closing stroke is different, and the installation dimensions include upward and downward expansion discharge valves. The opening and closing stroke is small, and the installation height is small. The installation height of the rotating rod structure is small, and the plunger only rotates during the opening and closing process. It needs to judge the opening and closing position of the valve based on the equipped opening and closing position indicator. The opening and closing torque of the upward spreading discharge valve is the upward movement of the valve disc. When opening, the valve needs to overcome the force of the medium, and the opening torque is greater than the closing torque.
What is the difference between the upper and lower discharge valves
The downward expansion and plunger type discharge valves move the valve disc downward and open the valve. When opened, the direction of movement is the same as the medium force, so the closing torque is smaller when opened.
Although there are great differences between the upward and downward spreading discharge valves, their common characteristics are that the valve seat is close to the end flange, the material retention is less, the structure is compact, and the sealing performance is superior. They are used in reaction pots in fine chemical, pharmaceutical, and chemical industries, and can also be used in the transportation of fine and soft particle media. Adopting PPL or M sealing materials, it is more wear-resistant and temperature resistant, making it an ideal product for the toothpaste industry and vacuum paste pot.